September 26th – – Bearings are considered as “joints” of industries.
Recently, the Liu’ao offshore wind farm in Zhangzhou, southeast China’s Fujian province, which features the application of 16-MW offshore wind turbine units, was put into full-capacity operation and connected to the grid for power generation. The bearings of the turbine units were independently developed in China.
Meanwhile, a tunnel boring machine equipped with a Chinese-manufactured main bearing, which comes with a diameter of over three meters, was instrumental in building the Suzhou Metro Line 6 in Suzhou, east China’s Jiangsu province.
These two bearings exactly mirror the solid strides in China’s manufacturing over the past 75 years since the founding of the People’s Republic of China.
The bearings used on the 16-MW offshore wind turbine units were produced by LYC Bearing Corporation. “We were incapable of producing high-end bearings over 10 years ago, but we were determined to crack this hard nut,” said Wang Xinying, chairman of the company.
To strengthen its capabilities, LYC set up Chinese national-level key laboratories and other innovative platforms. It also cooperated with Tsinghua University and other institutions of higher learning to leverage their strength.
As a result, it launched a wide range of new products, such as bearings for new energy vehicles (NEVs), wind turbine units, and for rail transit. These products have been employed by important equipment such as the Chang’e series lunar probes, the Tiangong Space Station, and the Five-hundred-meter Aperture Spherical Radio Telescope (FAST).
While LYC is striving for excellence in manufacturing high-end bearings, China Railway Construction Heavy Industry Corporation Limited (CRCHI) is focusing all of its energy on the development of tunnel boring machine (TBM) bearings.
In 2019, CRCHI set up a dedicated research and design institute to develop main bearings for TBMs, the “final piece of the puzzle” in China’s goal to fully localize its TBM industry. After three years, the institute finally developed a TBM bearing with a diameter of over nine meters.
“This main bearing, the largest and heaviest in the world, can be used in the largest TBMs currently available,” said Liu Feixiang, CRCHI’s chief scientist.
“In the past, what we could do was decided by what equipment we had, but now we can manufacture equipment for whatever task is needed,” Liu added.
Behind the two bearings lies the strong confidence stemming from China’s complete manufacturing system.
In 1949, China’s first batch of molten steel was produced by Ansteel in northeast China, and today, China has maintained the world’s largest steel producer for 28 consecutive years, constantly breaking world records in the thickness of steel foils.
In 1956, the first Jiefang truck rolled off the assembly line of Chinese automaker FAW Group. Today, China has been the world’s largest auto production and sales country for 15 consecutive years, while its production and sales of NEVs topped the global market for the ninth year in a row.
China has completed in a just few decades the industrialization process that took developed countries several hundred years. It boasts the world’s most comprehensive industrial categories and a well-rounded industrial system, with its manufacturing spanning 31 major categories, 179 subcategories, and 609 branch categories. For 14 years in a row, the country has remained the world’s top manufacturing hub. In 2023, its value-added manufacturing output accounted for 26.2 percent of its GDP and approximately 30 percent of the global output.
As Chinese enterprises constantly improve their capabilities and extend to the higher end of the industrial chain, more bearing products are hitting the market.
On March 10, a bearing developed by LYC for a 40-meter-aperture radio telescope in the Changbai Mountain area, northeast China’s Jilin province, completed acceptance inspection to support future lunar and deep-space probe missions.
On March 14, the world’s first main bearing for 25 MW wind turbine units successfully rolled off the production line at Luoyang Bearing Science and Technology Co., Ltd. in Luoyang, central China’s Henan province, setting a new record for the highest single-unit capacity in wind turbine bearings.
As products become higher-end, production must also become smarter. CRCHI has built a digital twin of the general assembly facility in one of its industrial parks in Changsha, central China’s Hunan province.
“This is a digital twin image of the front of a TBM’s cutterhead. The varying shades represent the stress and wear on the blades,” said Wang Yongsheng, deputy head of CRCHI’s digital twin research institute. By analyzing the data in real-time, engineers can upgrade the next-generation products in a more targeted manner, Wang added.
In China, mass-produced power battery cells now have an energy density of 300 watt-hours per kilogram, placing them at the forefront of international standards. The silicon-perovskite tandem solar cells made in China have achieved an efficiency of 34.6 percent, continuously setting new world records.
Besides, recent years have seen rapid growth in China’s export of “the new three,” namely, NEVs, lithium-ion batteries and photovoltaic products, with annual exports exceeding 1 trillion yuan ($140.93 billion).
Currently, strategic emerging industries account for about 13 percent in China’s GDP, and China is home to 463,000 high-tech companies. Chinese manufacturing is rapidly advancing toward the high end of the global industrial chain.
Moreover, the penetration rate of digital R&D and design tools in major Chinese enterprises reached 80.1 percent, and 62.9 percent of their key production processes are numerically controlled. Industrial internet has been applied in all major industrial categories, and the steps of industrial digitalization and digital industrialization have been accelerated.
By upgrading traditional industries, expanding emerging industries, and planning for future industries, China is developing new quality productive forces tailored to local conditions, continuously creating new drivers of growth and competitive advantages.
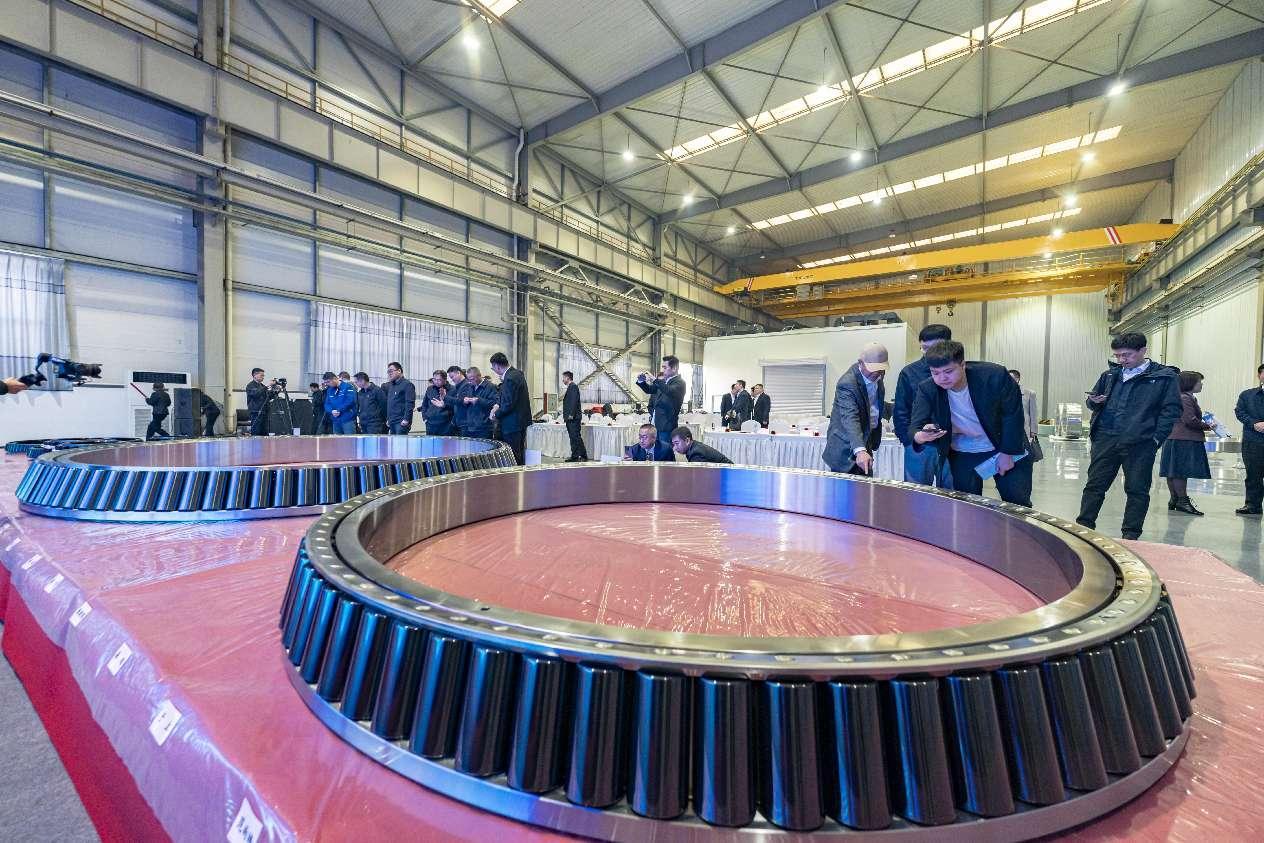
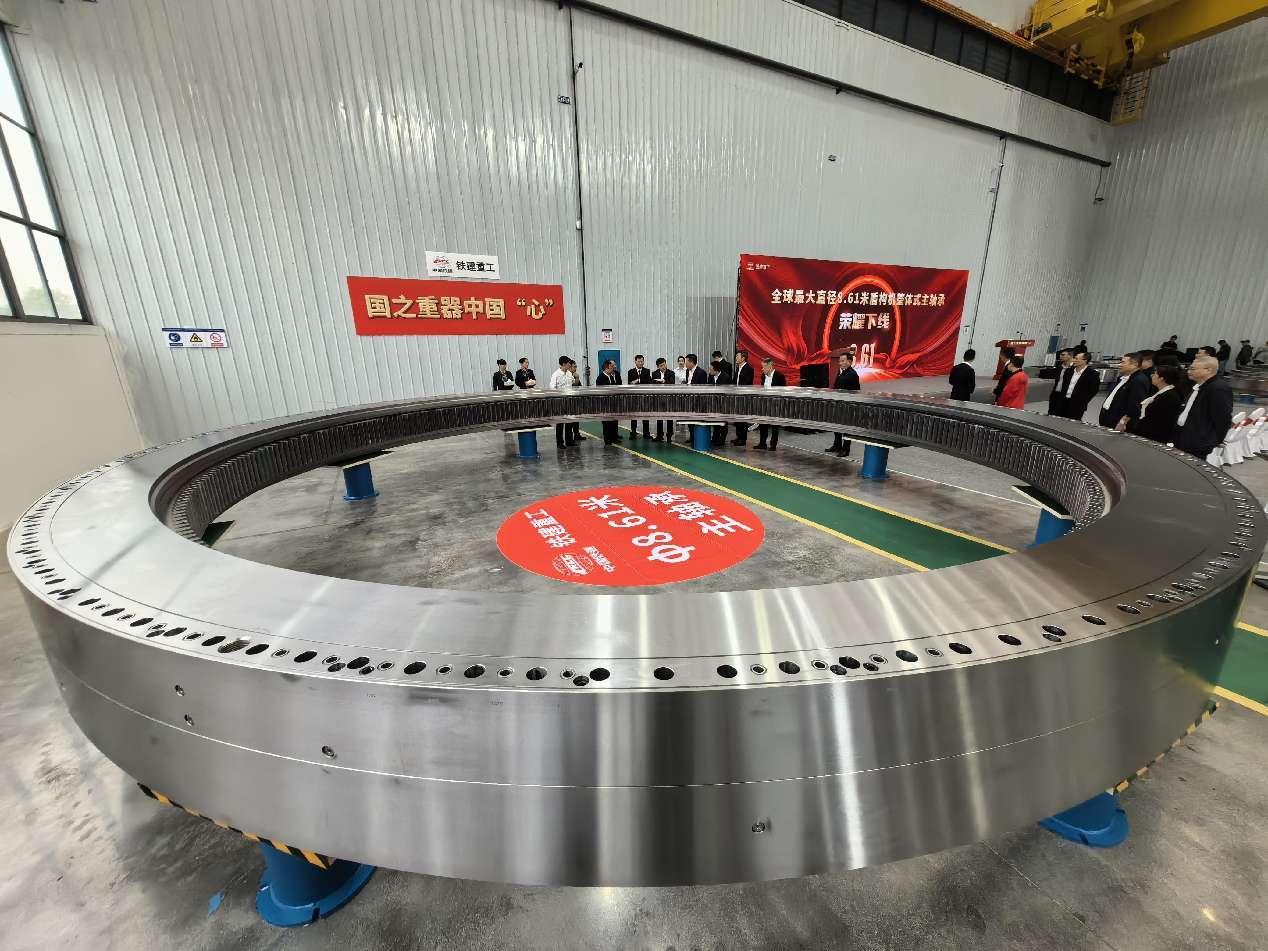
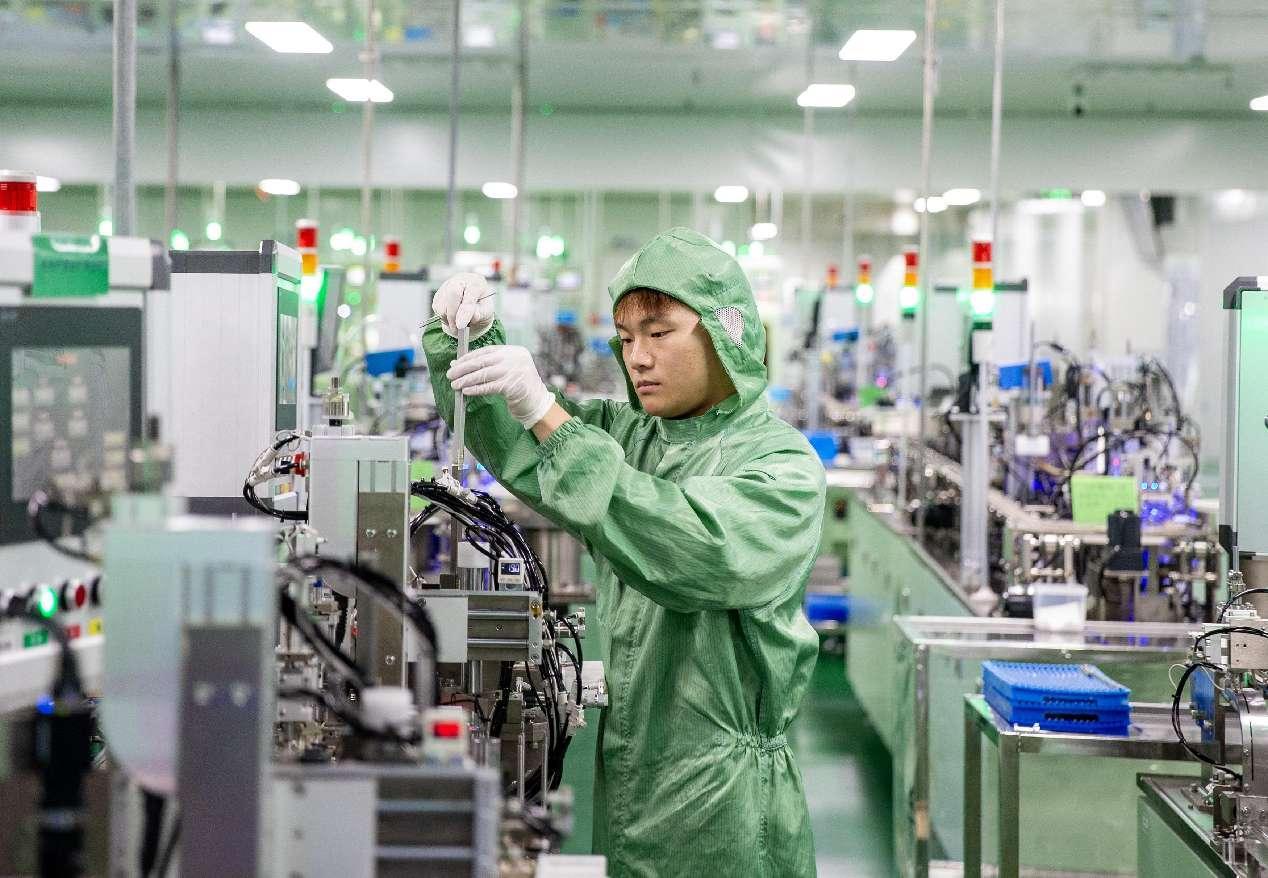
By Li Xinping, Wang Zheng, Ding Yiting, People’s Daily
Source: Global Times Online